Defoamers: Key Solutions for Managing Foam in Various Processes
Defoamers: Key Solutions for Managing Foam in Various Processes
Blog Article
The Function of Defoamers in Enhancing Product High Quality and Performance
Defoamers serve as crucial additives that mitigate this concern, guaranteeing smoother production process while enhancing the visual and functional features of the final items. The choice of the proper defoamer can be vital to attaining ideal outcomes, elevating essential questions regarding formula compatibility and performance metrics that warrant additional exploration.
Recognizing Defoamers
Recognizing the function of defoamers is crucial for keeping product high quality across different industries. Defoamers are chemical ingredients created to stop the formation and lower of foam in fluid systems, which can negatively influence processes such as mixing, filling, and surface stress. Lathering can bring about ineffectiveness, product defects, and jeopardized visual allure, making defoamers an essential element in producing operations.
In commercial applications, defoamers assist to boost item consistency and security. The reliable usage of defoamers not just guarantees smoother production procedures however likewise contributes to superior product efficiency.
Additionally, the option and formulation of a defoamer need to line up with certain application requirements, such as compatibility with other ingredients, efficiency under differing temperature and pH conditions, and prospective regulative restraints. Ultimately, recognizing defoamers' functions and their relevance in numerous formulas is vital for optimizing production and ensuring the finest quality final result.
Sorts Of Defoamers
Defoamers can be classified into a number of types based upon their composition and device of action. The key types include silicone-based, non-silicone natural, and not natural defoamers.
Silicone-based defoamers are among one of the most reliable, largely because of their ability to spread quickly on the liquid surface area and interrupt foam formation. Their one-of-a-kind chemical structure permits superior security, making them appropriate for high-temperature applications and environments with differing pH levels.
Non-silicone natural defoamers, often composed of all-natural oils or fats, are valued for their biodegradability and reduced toxicity. These are normally used in food and drink applications where safety and ecological impact are critical.
Not natural defoamers, that include compounds like talc or calcium carbonate, act by boosting the thickness of the fluid, consequently reducing foam security. They are typically made use of in industrial processes where compatibility with various other materials is not a concern.
Each sort of defoamer has distinctive advantages and limitations, enabling tailored solutions depending on the particular frothing problems come across in different applications. Understanding these distinctions is crucial for optimizing efficiency and accomplishing preferred product top quality.
Applications Throughout Industries
Various industries utilize defoamers to improve product top quality and operational efficiency. In the food and drink industry, defoamers are essential in procedures such as brewing and dairy manufacturing to avoid foam formation, which can bring about ineffectiveness and product incongruity. By managing foam, makers can make sure better return and a more uniform product.
In the pharmaceutical market, defoamers play a vital duty in the formula of fluid medications, where too much foam can hinder blending and accurate application. Their usage aids maintain the honesty of the formulas and promotes smoother production procedures.
The paint and coverings sector also relies upon defoamers to improve the performance of items throughout application. By reducing foam, these ingredients ensure a smoother surface and boost the aesthetic high qualities of the last item.
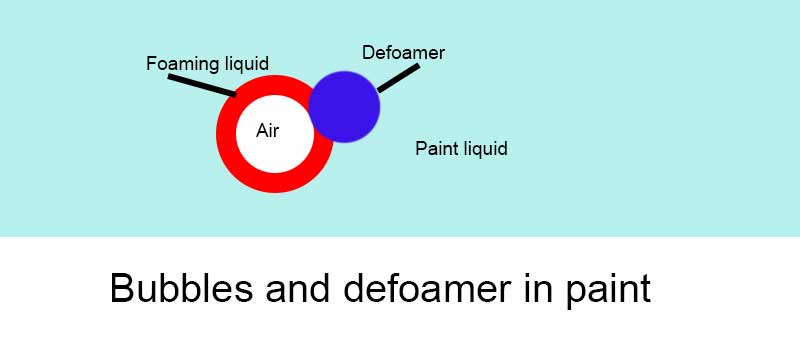
Advantages of Utilizing Defoamers
While the application of defoamers differs across markets, their benefits regularly enhance product top quality and procedure performance. One considerable advantage is the reduction of foam formation throughout making procedures, which can otherwise result in production hold-ups and incongruities in item high quality. By lessening foam, defoamers allow a smoother flow of materials, facilitating extra reliable operations and minimizing the possibility of equipment breakdowns.
In addition, making use of defoamers can improve the look and texture of end products. In fields such as coverings, paints, and food processing, extreme foam can compromise the aesthetic aesthetic appeals and total high quality, while the suitable defoamer application ensures a consistent finish and preferable attributes. Additionally, defoamers can contribute to set you back savings by lowering waste during manufacturing and optimizing using basic materials (defoamers).
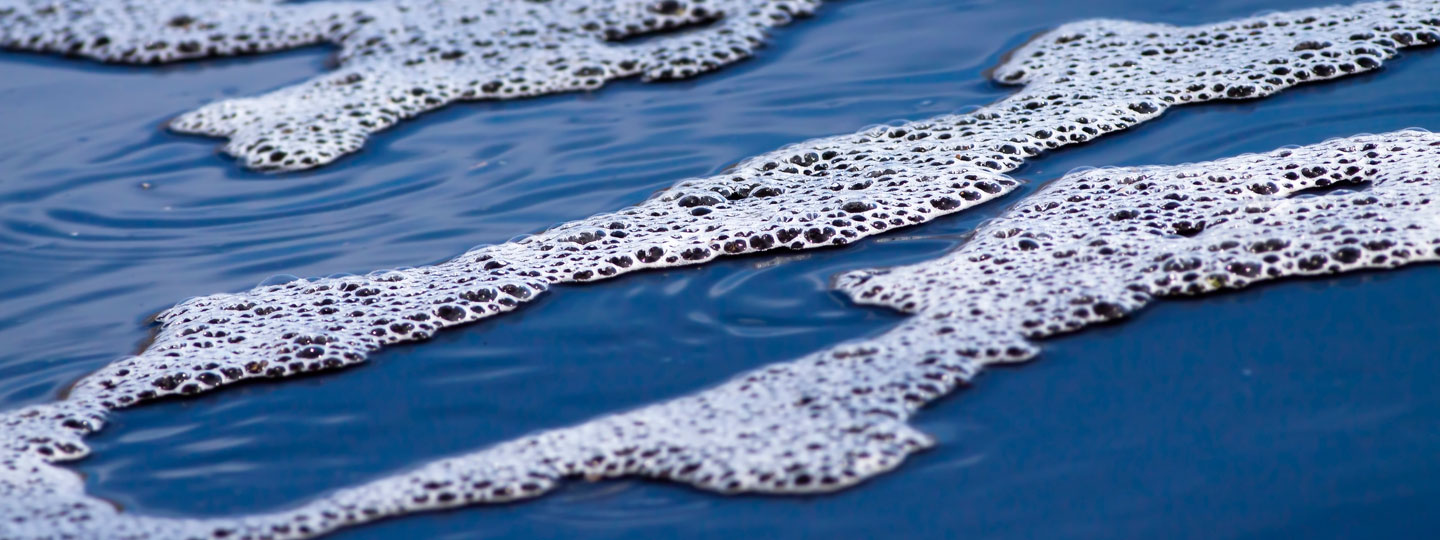
Choosing the Right Defoamer
Choosing the ideal defoamer is vital for maximizing manufacturing procedures and making sure item high quality. The option of defoamer influences not only the effectiveness of foam control but also the total efficiency features of the end product. Elements to consider include the sort of application, the chemistry of link the solution, and the ecological conditions under which the item will certainly be utilized.
Different sectors might need particular read this post here defoamer types, such as silicone-based, natural, or polymeric defoamers. Comprehending the compatibility of the defoamer with the main ingredients is vital to avoid damaging reactions that could endanger product integrity. In addition, the defoamer's efficiency in various temperature levels and pH degrees should be evaluated to make sure constant efficiency.
Evaluating the defoamer in small applications can offer beneficial insights right into its performance and suitability. Factor to consider of regulatory conformity, especially in food, drugs, and cosmetics, is paramount in choosing a defoamer. Inevitably, a complete assessment of these elements will certainly result in the choice of a defoamer that not just controls foam successfully yet likewise improves the top quality and performance of the last product.
Final Thought
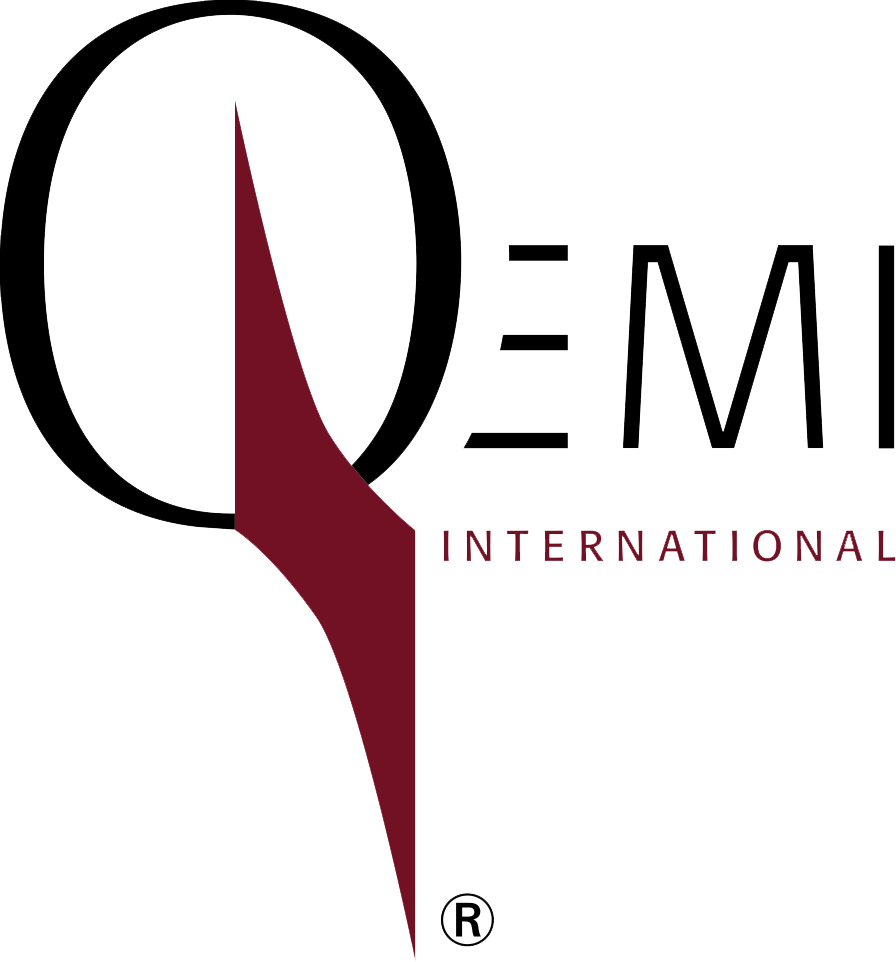
To conclude, defoamers are crucial ingredients that considerably enhance item quality and performance across different markets. By properly reducing foam formation, these agents not only boost functional performance yet also add to the practical and visual honesty of items. The critical option and application of defoamers bring about set you back financial savings, optimized resource use, and enhanced consumer contentment. On the whole, the relevance of defoamers in commercial processes can not be overstated, as they play a vital duty in accomplishing constant and top notch end results.
Lathering can lead to inefficiencies, item flaws, and jeopardized visual allure, making defoamers a vital component in making operations.
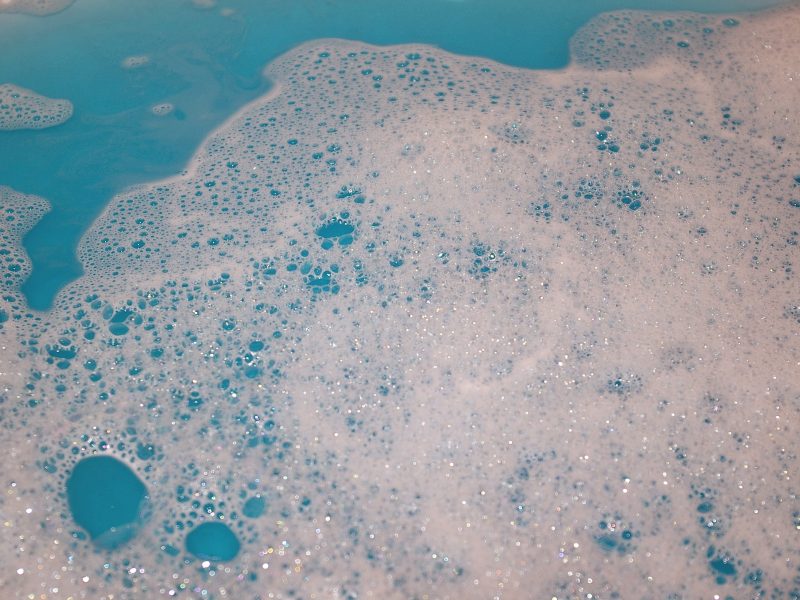
Report this page